Article | November 8, 2022
Download as a PDF document
What is a Cooling Tower? A cooling tower is a device or structure that cools water that was used to remove heat from an industrial process or from air conditioning equipment.
Cooling towers are heat exchangers, using airflow and meticulous design to take in hot water, cool it down, and return it to the industrial process to remove more heat.
They can be huge, rising above the buildings of an electrical generating station, or small enough to be part of a building’s roof design.
How Does a Cooling Tower Work?
There are different types of cooling towers, but they rely on the same principle: evaporative cooling. Evaporative cooling is the process by which the evaporation of water removes heat from a system, similar to how heat is removed from the body through perspiration.
Jets inside the cooling tower convert water that has been warmed from industrial processes into droplets. Those droplets are then sprayed into what’s called the “fill media,” which is typically textured sheets of PVC that catch the droplets and spread them out.
At the same time, cool, dry air is being pulled into the tower by fans. Droplets have more surface area than large amounts of water, so when the cool air hits the droplets, it cools them rapidly - removing heat from the water by evaporation. Cooling tower fans then expel the hot air produced by evaporation from the top of the tower.
As the water cools down, it is routed back to where it started. The process of heating up and cooling down is repeated again and again, so the water can be reused in a continuous loop.
Which Industries Use Cooling Towers and Why?
Cooling towers are used in a variety of industries for different applications. Because they’re so much larger than traditional rooftop packaged HVAC systems, the industries in which they’re used are also larger than typical homes, schools, and businesses. Such facilities include power generation stations, food and beverage process facilities, as well as industrial manufacturing facilities.
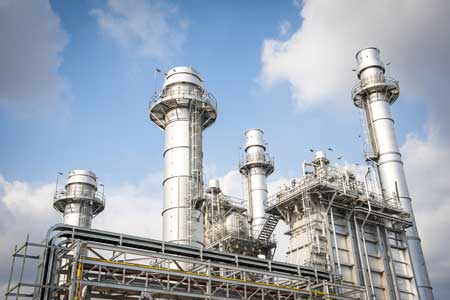
Applications and Geographies Requiring Efficient Control of Heat Exchanges
There are some specific applications and geographies in which the cost of water consumption or other variables govern the process for the most efficient control of industrial heat exchanges, those are:
Industrial Cooling and Process Water
Most cooling towers rely on municipal wells or similar municipal water systems, which means monitoring water usage with pinpoint accuracy is vital.
Commercial HVAC Cooling
Hospitals, hotels, and other 24/7 commercial operations rely on cooling towers and proper metering to ensure consistent performance without the risk of shutdowns.
Water-restricted Geographies
Certain areas, such as desert environments, often have strict water usage and conservation rules that commercial businesses need to abide by. These businesses rely on accurate, reliable cooling tower water measurement to meet those regulations and operate efficiently.
Cooling towers are also used in:
- Industrial manufacturing
- District energy
- Pulp and paper
- Pharma and chem
- University campuses
Types of Cooling Towers
There are many different types of cooling towers, and they’re not necessarily interchangeable among applications. Often, a cooling tower is designed for a specific use. Details aside, all cooling towers have the same basic function: to reduce the temperature of hot water for use in an industrial process in the most efficient manner possible.
Different geographical regions may employ different types of heat exchanges, but the variations don’t have any bearing on the metering points or the benefits of metering in this application.
Some of the varieties include:
• Crossflow cooling towers
Crossflow cooling towers bring water into the fill media vertically while at the same time, air flows horizontally across the water as it falls; hence, a cross flow of water and air.
• Counterflow cooling towers
Counterflow cooling towers push air up as hot water flows down. Air and water are flowing against each other—counter to each other. These systems also use a pressurized spray to move water instead of relying on gravity basins as crossflow towers do.
• Forced-draft and induced-draft cooling towers
Forced-draft and induced-draft cooling towers use a fan to move hot and cooled air through the tower. The difference between them is where the fan is placed. In a forced-draft system, the fan is at the base of the cooling tower. In an induced-draft system, the fan is at the top of the cooling tower.
• Factory-assembled (FAP) and field-erected (FEP) cooling towers
FAP cooling towers are built in the factory and shipped at least partially disassembled for final assembly on-site. In contrast, FEP cooling towers are fully assembled on-site. FAP and FEP cooling towers can be either crossflow or counterflow.
• Natural-draft and mechanical-draft cooling towers
Natural-draft and mechanical-draft cooling towers differ in the way air moves through the tower. In a natural-draft system, hot air rises through the tower and is released. The shape of these towers encourages airflow upward.
In a mechanical-draft system, air is forced through the tower with a fan. They’re more effective but also use more power than the natural-draft model.
The Importance of Cooling Water Management
Cooling towers are useful only if they’re properly managed and treated. Efficient operation requires the use of key chemicals to combat corrosion, microbiological contamination, and fouling, and the proper dosages depend on accurate information about the system and blowdown water.
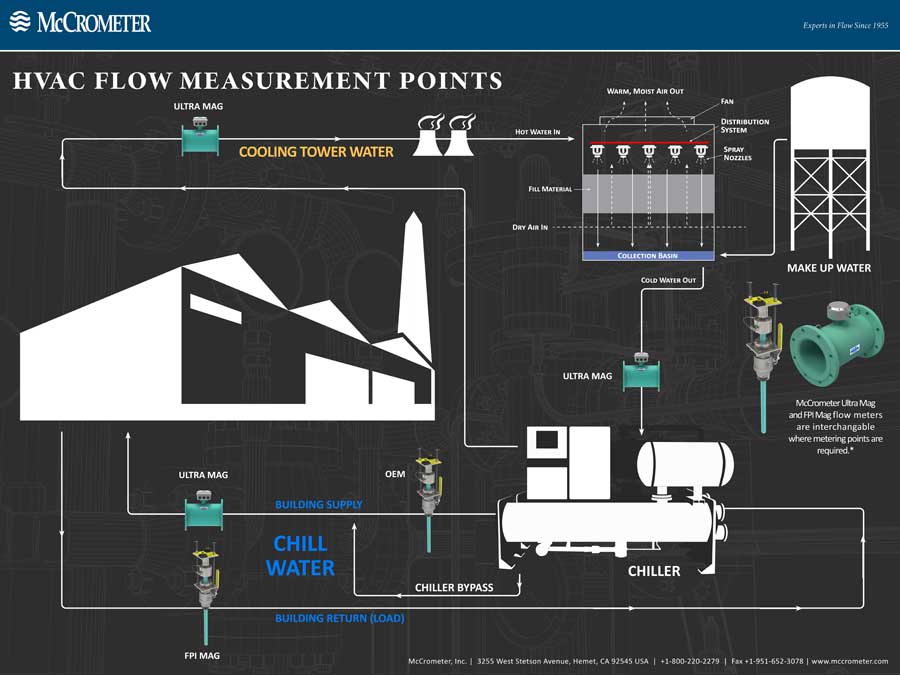
It is essential to use an accurate flow meter in a cooling tower in order to control chemical costs and ensure reliable flow results. A flow meter is an important tool in maintaining proper design flow and providing adequate cooling.
Without Flow Meters, Cooling Water Can Impact Equipment, Climate Control
Without flow meters, insufficient cooling water can impact equipment or climate control. If the water level is too low, the pipes suck in air. If the water level is too high, the water will overflow, which can cause damage to the roof of the tower as well as leaks.
Efficient water and cooling tower management is so essential, in fact, that there are government and regulatory rebates and programs to incentivize efficient water and cooling tower management.
For example, the U.S. Green Building Council provides two points toward LEED certification with proper cooling tower management strategies.
Accurate Flow Measurement Data Is Key
The only way to efficiently manage a cooling tower system is to have accurate data, since you can’t manage what you don’t measure. Effective resource measurement is good for a company’s reputation and commitment to sustainability.
Flow measurement is a data output that can affect daily operations, as the rate of flow in and out of the cooling tower affects the dosage of water treatment. Operators and engineers cannot accurately dose the water with chemicals without an accurate measurement of inputs and outputs for their towers. Dosing water with the wrong type or amount of chemicals is an expensive fix that can cause process shutdowns or affect the biological integrity of the water supply.
How to Optimize Cooling Water Management and Lower Plant Operating Costs
There are ways to collect the data you need to effectively manage a cooling tower’s operations and efficiency. First, be sure to install flow meters in the proper locations. For applications that require the use of chemical dosing pumps, be sure to install the flow meters upstream from the pumps.
This ensures that the chemicals won’t affect the meter’s ability to provide accurate flow data that can alert the system to low flow situations, which can lead to pump problems. In applications that do not require chemical dosing pumps, however, flow meters should be installed downstream from pumps.
It is also important to use flow information from the blowdown and make-up water lines to calculate rates of evaporation, cycles of concentration, and cooling water chemical treatment rates to quantify tower efficiency and effectiveness.
McCrometer Flow Meters for Cooling Tower Water Management
Not all flow meters are created equal, and not every meter is right for every application. Variables include the fluid as well as the usage, and both cooling towers and HVAC systems are required to measure flow to +-0.5% accuracy.
Having the correct equipment for your system is essential to cutting down on maintenance issues and ensuring a long life. McCrometer can make it easier.
Our FPI Mag ® and Ultra Mag meet cooling tower accuracy requirements and can be
FPI Mag ®
The FPI Mag is the full-profile insertion mag meter ideal for new and retrofit projects.
Ultra Mag ®
Advanced mag meter for industrial and wastewater, resists clogs and corrosion.
The FPI Mag in particular, offers a wide range of benefits, including hot-tap capability. The simple installation process means the meter can be installed without any disruption to the system’s service or its customers and without labor-intensive actions such as cutting pipe or welding flanges. It is the only full-profile insertion magnetic flow meter on the market.
The benefits of both the FPI Mag and the Ultra Mag meters include:
- Ability to measure flow to +- 0.5% accuracy
- Zero to low straight-run requirements
- Cost-effective, with a five-year warranty on the meter and battery
- Custom lay lengths
Both meters are ideal for a range of needs, including:
- Chill water supply
- Chill water return
- Cooling tower supply
- Cooling tower return
Contact McCrometer to learn more about how flow meters can optimize cooling water management for industrial cooling and process water applications.