Article | January 31, 2023
Download as a PDF document
Water and wastewater professionals rely on accurate flow measurements for process operation and regulatory compliance. Selecting the best flow meter for each application is essential to obtaining accurate flow data.
A starting point is detailed knowledge of the application and the fluid being measured. It’s also necessary to understand the characteristics of different meter types to determine a best fit. Electromagnetic meters and ultrasonic meters are popular for use in the water industry. Below is a comparison of these two meter types to assist with decision-making.
Electromagnetic Meters vs. Ultrasonic Meters Applications and Limitations
- Operating Principles
- Applications and Limitations
- Installation Factors
- Maintenance
- Accuracy
- Cost
- Choosing the Best Meter for Your Application
- Featured Electromagnetic Meters
Operating Principles
Electromagnetic flow meters , called mag meters, operate on the principle of Faraday’s Law. This principle basically states that as a conductor, such as water, moves through a magnetic field it produces an electrical signal. Full-bore mag meters use an electromagnet mounted on the outside of the pipe, perpendicular to the flow direction. As flow passes through the magnetic field, electrically charged ions accumulate, with negative ions on one side and positive on the other. The resulting change in voltage is directly proportional to the velocity of the fluid passing through the pipe, which can be converted to volume.
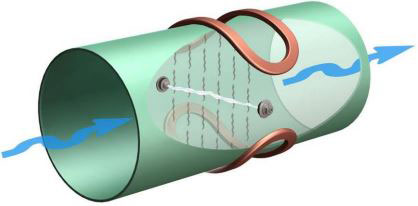
• View McCrometer’s Electromag Product Suite
Insertion mag meters operate a little differently. For an insertion meter, a very small, localized magnetic field is inserted into the pipe. Electrodes cause charge bearers to separate. With a full-profile insertion meter, electrodes are located along the entire cross-section of flow to measure average velocity across the pipe centerline.
Ultrasonic flow meters use sound waves to measure the velocity of fluid flowing through a pipe and convert that data to volume. Two basic types of ultrasonic meters are transit-time and Doppler meters.
Transit-time meters send ultrasound signals into the flow using transducers that are either clamped onto or inserted into the pipe at two locations. The difference between the time it takes for sound to travel upstream and downstream between the two sensors is directly proportional to flow velocity.
Doppler meters use sound waves reflected off materials in the fluid, such as air bubbles or particulates, to measure flow velocity.
Applications And Limitations
Both mag meters and ultrasonic flow meters can be used for various water and wastewater applications, including measurement of sludges, slurries, and some chemicals.
Mag meter performance is not affected by temperature, pressure, or viscosity. These meters can handle rapid changes in flow. They can accurately measure clean fluids like drinking water or those with heavy solids like sewage lift stations and biosolids facilities. However, mag meters cannot measure non-conductive fluids like oils, steam, or gases. Mag meters can measure flow going vertically or horizontally. With today’s high-resolution microprocessors, they can measure flows as low as 0.2 to 0.3 feet per second.
Transit-time ultrasonic meters can measure conductive and non-conductive fluids. These meters may have problems measuring fluids with suspended solids, debris, or air bubbles, which interrupt the path of the sound signal. Temperature compensation may be required to maintain accuracy. Corrosion, pitting, or biofilm buildup on the pipe wall can cause problems as well.
Doppler meters need some type of material — air bubbles or solids — in the stream to measure flow.
Installation Factors
Ultrasonic and mag meters can both be installed on a wide variety of pipe materials and sizes, from ½-inch to over 100 inches in diameter.
For tight sites or retrofit projects, mag meters require less straight pipe to avoid inaccuracies from flow disturbers. A full-bore mag meter only needs one diameter length upstream and two downstream, whereas the ultrasonic meters typically need 10 upstream and five downstream.
Insertion-type mag meters offer the ability to install the meter with a hot-tap for cases where shutting down the process is undesirable.
An important consideration for mag meter installation is to ensure an electrically quiet atmosphere, with good grounding and shielded cables.
Transit-time ultrasonic meters can be clamped on or hot-tapped into the pipe. Coatings must be removed from the outside of the pipe and a material added between the pipe and sensor. The exact thickness and material of the pipe must be known in order to obtain desired accuracy.
Maintenance
Mag meters have no moving parts and require no maintenance.
Ultrasonic meters are also devoid of moving parts. The clamp-on types require a material between the sensor and the pipe to properly transmit the sound. This material degrades over time and needs replacement. Also, the clamps must occasionally be tightened.
Both types of meters have problems with lightning strikes and power surges.
Accuracy
Mag meters are highly accurate, with inaccuracies of ±0.5 percent of rate or less. In comparison, transit-time ultrasonic meters have inaccuracies of ±1 to 2 percent of rate.
Cost
Cost comparisons depend greatly on the specific project rather than meter cost. Both meters can provide cost-effective flow measurement. Would the project use a full-bore mag meter or insertion type? A transit-time ultrasonic or Doppler? The additional straight pipe needed for ultrasonic meters could add extensive capital costs.
The higher accuracy level of the mag meters combined with minimal straight pipe requirements and long life provide a very low lifecycle cost. A New York City mag meter installation from 1920 is still working and providing accurate flow data.
Choosing The Best Meter For Your Application
Both mag meters and ultrasonic meters provide highly accurate flow readings for water and wastewater applications.
However, the mag meters provide a higher level of accuracy and more flexibility. Mag meters are available for full-bore installations but can also be provided for instances where hot-taps are needed to avoid process shutdown. A full-profile insertion mag meter provides the high accuracy level of a full-bore installation without the need to cut into an existing pipe.
For retrofit projects or those where space is limited, the need for only one diameter length of straight pipe upstream and two downstream lowers capital costs and makes life easier.
With no maintenance requirements and extremely long operating life, mag meters have low lifecycle costs for dependable, accurate flow measurement.
Ask For Technical Assistance
Water professionals shoulder the responsibility for protecting the public health and the environment. Accurate flow measurement is an important part of process operation. Choosing the right flow meter saves time, money, and headaches.
Manufacturers’ representatives have deep knowledge and experience that can help in making the right decision. Ask for their assistance when deciding which meter works best for your project.