Know Your Options For Mag Meter Installation Cost, Care, and Calibration
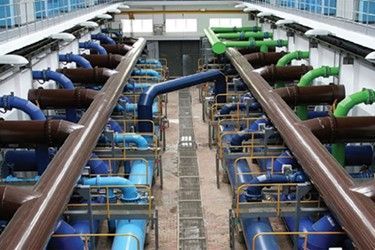
Electromagnetic meters (mag meters) are well established in terms of highly accurate performance for a variety of municipal and industrial water applications. Differences in their construction formats, however, dictate how easy they can be to install, maintain, and calibrate. Compare these three options to see the value of full-profile-insertion (FPI) mag meters and their associated advantages in real-world use.
Selecting The Right Execution For The Flow Project At Hand
Because all mag meters share a common technology based on Faraday’s Law, their operation is reliable and relatively unaffected by turbulence-inducing conditions. Different product construction formats, however, create performance characteristics that make some designs better suited for certain applications.
- Full-Bore Mag Meter. This design creates an electromagnetic field within a pipe cross-section to deliver + 0.5-percent flow measurement accuracy. As a non-invasive design that leaves the pipeline cross-section completely unobstructed, it accommodates fluid ranging from clean water to wastewater influent and even waste-activated sludge. While its flanged format is reasonably convenient to install in new construction, replacing it or removing it for calibration in a continuous operation can become problematic and expensive, especially as pipeline size increases (Figure 1). This can become even more difficult in vaults and other hard-to-access locations and is particularly challenging for large line sizes.
- Insertion Mag Meter — Full Profile. This design senses flow at multiple locations across the full diameter of the pipe to deliver long-term accuracy to + 0.5 percent in clean water conditions (Figure 2). Hot-tap installation and maintenance convenience can save 45 percent on installation and total cost of ownership as compared to full-bore mag meters.
- Insertion Mag Meter — Single Profile. While affordable single-profile insertion mag meters do offer hot-tap convenience, their single measurement location limits accuracy to + 2 percent of scale because it cannot account for flow variations across the entire cross-section of the pipe (Figure 3).
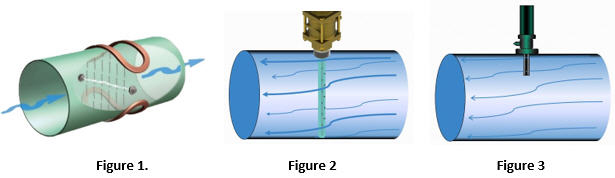
Experiencing Full-Bore Accuracy With Increased Benefits
FPI mag meters deliver the same high accuracy of full-bore mag meters but with a much lower total cost of ownership across multiple aspects:
- Convenience. In continuous operations such as water treatment and distribution, where shutdowns are avoided at virtually any cost, hot-tap installation capability is a great advantage. By their very design, FPI mag meters easily adapt to preexisting pipeline configurations where other styles of meters simply cannot fit. This includes existing water treatment and distribution installations where mounting space is limited, or where turbulence created from nearby upstream elbows, pumps, valves, or step-down fittings is a problem.
- Complexity. As pipelines grow larger, full-bore mag meter replacement gets more complex in terms of the logistics associated with large flange-mounted spool pieces — excavation, rigging, cranes, welding expertise, the need for ‘perfect fit’ sizing, etc. By contrast, hot-tap mounting of FPI mag meters — using standard 2”-NPT fittings on pipe sizes from 2” through 120” — minimizes time commitments and out-of-pocket expenses for heavy equipment rental or contracted installers.
- Labor. Because personnel at many water utilities are very familiar with hot-tap installation procedures, even the largest FPI mag meters can be installed in just hours with just a couple of workers. Compared to flanged, spool-type full-bore mag meters, they minimize installation time, labor, and rigging costs — without disrupting normal water distribution operations.
- Speed. All of the above advantages add up to being able to hot-tap install an FPI mag meter in a 72” pipeline in a matter of hours — without disrupting system operation — as compared to a two-day shutdown for a comparably sized full-bore mag meter. In fact, FPI mag meters are often retrofitted into existing applications adjacent to decommissioned full-bore mag meters, without even bothering to remove the old meters.
- Lifecycle Cost. Once installed, an FPI mag meter can be the gift that keeps on giving — in terms of operation, maintenance, and calibration costs and efforts.
Avoiding Service Disruptions
Eliminating the need to shut down service is not restricted to initial installation alone. That benefit is magnified every time an FPI mag meter is removed for cleaning or calibration. Hot-swapping a backup meter in place of the original meter to be serviced takes significantly less time, without compromising pipeline pressure and with minimal disruption to data collection.
Minimizing Maintenance Time, Effort, And Money
Under normal use, there is not typically a need for frequent maintenance or calibration of an FPI mag meter, but when there is, the ease of removing it from its ball-valve mount makes the process a quick one.
While there are no hard and fast rules regarding service intervals, users might want to establish their own schedule based on the fluid conditions in the pipe — i.e., minerals, dirt, corrosion, iron, or other water chemistry. One good strategy is to try progressively longer intervals based on the results observed. Start with a three-month period. Double that to six months if there are no fouling or calibration issues. Then double that to 12 months, and so on, if there are no subsequent issues.
Simplifying Calibration Requirements
Where there is a regulatory requirement to recalibrate water treatment or water distribution meters — such as documenting water loss in water-scarce environments — easily swappable FPI mag meters speed the process of compliance. Units can be easily swapped out with a backup model and shipped to a NIST-traceable calibration lab.
By comparison, in-situ calibration of full-bore mag meters can incur added costs for outside calibration services and can even compromise accuracy if the comparison meter being used — e.g., a strap-on ultrasonic meter — has trouble with any turbulence caused by the upstream piping configuration.