Monitor Cooling Tower Water Consumption Accurately, Without Disruption
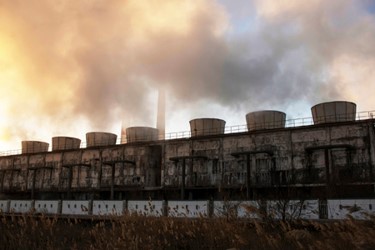
Operations that want to track cooling tower water use accurately in 24/7 applications — without having to disrupt processes to install a new meter — need options that are easy to retrofit into continuous operations. Here’s how they can achieve + 0.5 percent flow meter accuracy without compromising cooling tower availability, by employing full-profile insertion (FPI) electromagnetic flow meters (mag meters) with hot-tap installation capabilities.
Cooling Towers — Industrial And Beyond
While cooling towers provide process cooling and HVAC capacity across a broad range of commercial activities, not all applications are identical. Where regulatory constraints or the costs of water consumption are high, however, the need for accurate measurement is critical. As a result, FPI mag meters are gaining acceptance in a variety of evaporative cooling tower applications due to their ability to satisfy both accuracy and installation concerns.
Here are three tips for using them to optimize cooling water management and lower operating costs in applications such as:
- Industrial Cooling And Process Water. While some older industrial uses were built to rely on large volumes of flow-through process cooling water from rivers or lakes, many of today’s industrial operations depend on cooling towers supplied by municipal potable water systems or wells. In those cases, issues of cost or withdrawal rates require accurate monitoring.
- Commercial HVAC Cooling. In some commercial HVAC cooling tower applications, it might be possible to schedule downtime to retrofit the water supply line with a new, more accurate meter. But in hospitals, hotels, and other buildings that use HVAC system cooling towers for total-building cooling systems, continuous operations are the norm. Buildings designed for LEED certification (Leadership in Energy and Environmental Design) are specifically concerned with efficient cooling tower operation and water use.
- Data Center Cooling. Another key application for high-volume cooling tower use is 24/7 data centers that support large volumes of computing equipment — such as cloud-hosting services or large corporate sites. Whether those sites are served by municipal water utilities or source their own water, the sheer volume of their requirements warrants accurate consumption tracking. In either case, such installations can ill afford any disruptions to their cooling capacity.
Evaluating Accurate, Affordable, Flow-Metering Solutions
In order to manage cooling water costs and availability, it is important to know the volume being consumed. The larger the cooling tower operation, the greater the stakes. For continuous operations that cannot afford shutdowns to install a new, highly accurate meter, however, physical implementation of the metering solution can be just as important as its accuracy. That is where FPI mag meters can provide the best of both worlds:
Figure 1. With electromagnetic sensing across the full diameter of the pipe, FPI mag meters offer extreme flexibility in mounting requirements without compromising the accuracy of readings under a variety of flow conditions.
- Accuracy. Electromagnetic sensors spaced along the entire length of an FPI mag meter probe provide accurate readings across the full diameter of the pipeline, regardless of flow profile or turbulence (Figure 1). This delivers + 0.5 percent accuracy at flow rates from 1 ft/s to 32 ft/s (0.3 m/s to 10 m/s) in line sizes up to 18”, to 20 ft/s at a line size of 30” and to 10 ft/s at a line size of 72”.
- Installation Convenience. With hot-tap installation convenience, there is no need to disrupt cooling tower operation to install a highly accurate new meter. Subsequent cleaning and recalibration can also be performed throughout the life of the instrument, as needed, without impact on continuous cooling tower operation. While most cooling tower applications will have access to AC current for meter operation, battery-powered and solar-powered units are also available for collecting data in more remote operations. Digital outputs can feed existing building automation systems, plant SCADA systems, and analytics systems to provide up-to-date performance statistics for informed decision-making. Many cooling tower feed lines are in the 6” to 8” range, but FPI mag meters are also available in line sizes from 4” to 138”.
- Installation And Operation Savings. Compared to conventional flange-mounted mag meters, FPI mag meters conserve cost and effort with simplified installation Here are some of the key differences:
- The convenience of hot-tapping reduces the time needed to install new or replacement metering capabilities in existing cooling tower water systems. Once the pipe is tapped and measurements of the inside pipe diameter are taken through the attached ball valve, final installation can be completed in as little as 20 minutes.
- Hot-tap installation eliminates the manual labor required for isolating lines, cutting pipe, and welding flanges. It also eliminates the back-end labor related to reactivating an exposed water system. These labor savings can minimize the need for hiring outside piping installation specialists and the administrative headaches of planning for and scheduling production shutdowns.
- Equipment Rental.The larger the flanged mag meter, the heavier the spool piece and the greater the likelihood of needing to use heavy-lifting equipment to install it. Most cooling tower FPI mag meters can be installed by a single maintenance worker.
- Reliable Performance. An FPI mag meter with appropriate heavy-duty, 316-stainless-steel construction, a hermetically sealed body, and fusion-bonded epoxy coating enhances the value of its low total cost of ownership by providing robust performance in the wet outdoor environments associated with many cooling towers.